COVID-19 & Supply Chains: 3 Tips for Medical Distributors to Respond to Supply Shocks
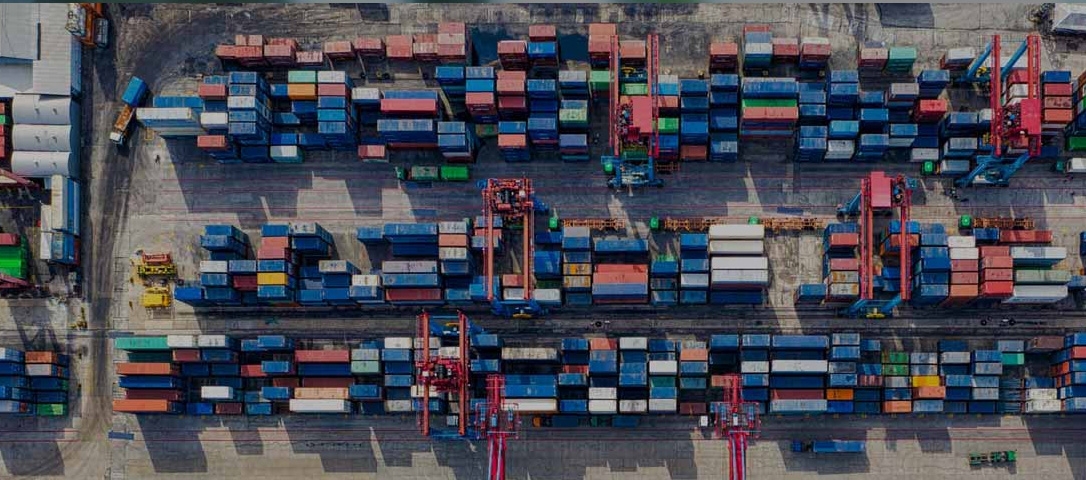
Contents Overview
The new virus pandemic was first felt by players, across all industries but especially those in medical, most involved in the supply chain sector. Faced with unique challenges, supply shocks started right after the first virus outbreak. Because of the interconnectivity of major parts of the global supply chain, a domino effect continued right after Wuhan went into lockdown. As the city is one of the world’s manufacturing hubs for finished products and many raw materials, demand shocks occurred soon after. To avoid problems with goods accessibility in the short run, manufacturers and distributors started overstocking. For this reason, it is abundantly clear China carries a dominant role as the ‘world’s factory’ with more than 200 of the Fortune Global 500 companies having a presence in Wuhan. Consequently, it is also clear that any major disruption there can put the worldwide supply chain at risk, and it has happened faster than anyone predicted.
However, knowing even a single supply chain disruption can reduce shareholder value by up to 7% (World Economic Forum), China's dominant role is bad news for the global economy. Fortunately, recent events awakened world supply, chain leaders. Even if the final outcome of the pandemic is not yet known, it is already certain that the global supply chains will never be the same. In fact, coronavirus pointed out the increasing need to transform the industry’s traditional models and address vulnerabilities the system has long been exposed to.
Single supply chain disruption can reduce shareholder value by up to 7%, the World Economic Forum reports
Yet, controlling new virus developments or changing the supply chain as a whole is not something small players like local medical distributors can do. And if preventing an outbreak is not likely for whatever reasons, mitigating risks and adapting to market opportunities and niches for their own businesses is most certainly the correct step forward. For this, realizing and admitting a distribution company faces a crisis is the first thing team leaders must do. Looking at key challenges, such as logistical disruptions, raw material shortages and changes in product demand should follow. By doing this, the coronavirus crisis just might unintentionally do something good – motivate even the smallest players to rethink their approaches and, as the saying goes “the whole is greater than the sum of its parts”, changes to the global supply chain model will be profound.
Key Challenge #1
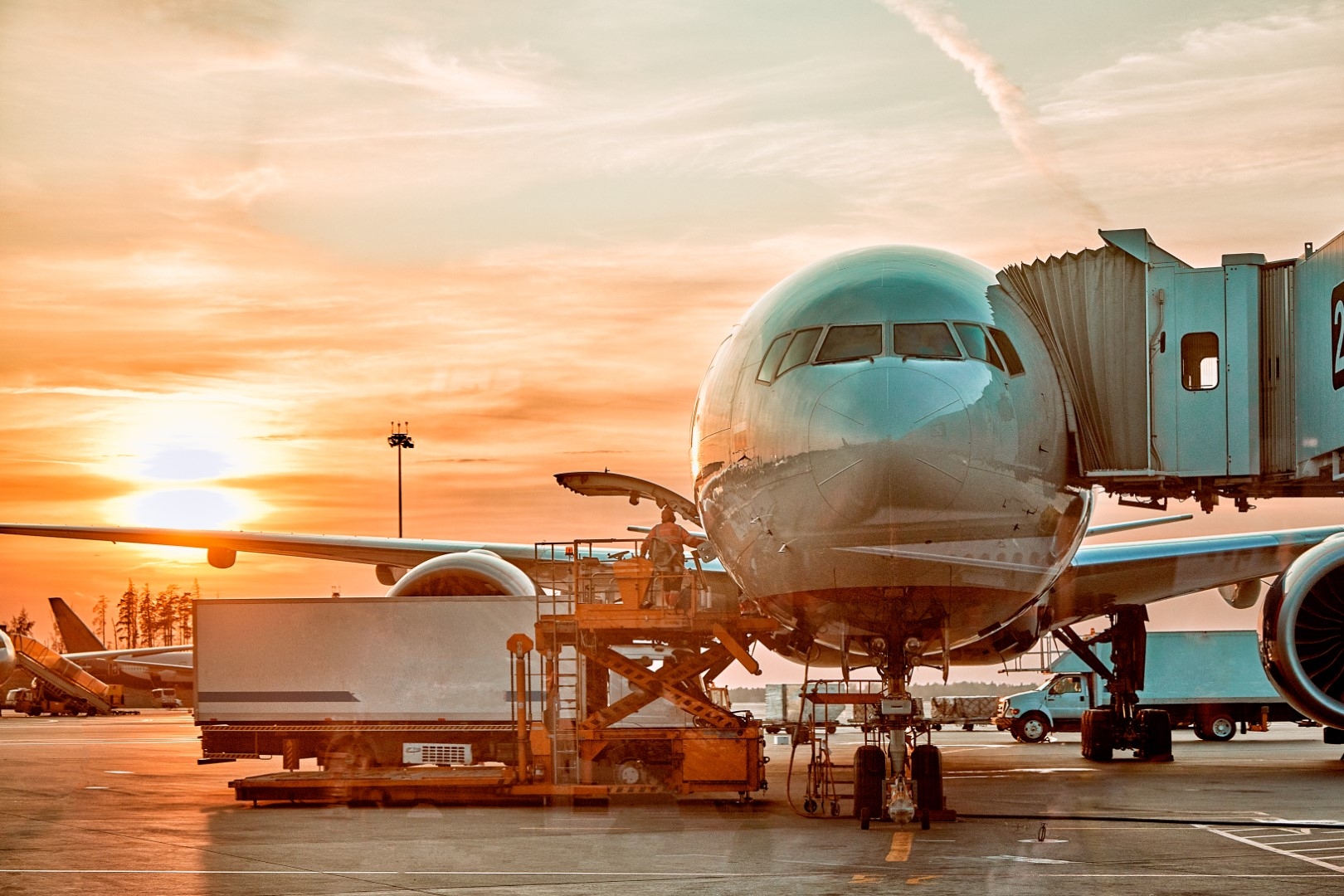
Logistical and Planning Disruptions
Logistic services were one of the first and most heavily affected by the Covid-19 outbreak. Not only that labor was not available to transport goods, but managers also had to face port congestion, a decrease in air freight capacity, and truck driver shortages. Furthermore, on production levels, many warehouses struggled to move the goods as national lockdowns affected the number of staff available. With a deficit in workers, even tasks like loading and unloading goods were difficult to handle in a timely manner. On the other side, delays were occurring also due to restricted border crossing, and sticker import rules or customs clearance processes. Even more drastically, Covid-19 has resulted in unprecedented planning disruptions as even some airspace has closed down and placed a major strain on essential linkages between regions. All of this resulted in many cases of congestion in the cargo flights and shipping vessels and a reduction in the number of transports carried out worldwide.
Since many logistic companies had to take on indirect routes to enable the execution of their services – delivery of goods – prices peaked as much as 400% over normal rates. Many experts now believe prices will not come down to pre-virus days even after restrictions of the pandemic are lifted. Coronavirus pandemic has, therefore, placed extraordinary demands on logistic leaders in different businesses. Even if in many parts of the world production is slowly beginning to get back to normal, it turns out that it now costs companies more to move the goods to its distributors.
Looking ahead, this may result in fundamental shifts in the industry footprint. Many companies will most likely consider moving a portion of their production capacities closer to their end markets, to avoid increasing logistical costs in similar situations in the future. On another note, it will be also smart for them to reassess risks and costs of production in today’s global supply hubs, such as China, known as ‘the factory of the world’. Vietnam, Indonesia, Thailand, Malaysia, Mexico, or India are likely to benefit from it. However one thing is clear, decentralization of manufacturing capacity and companies looking to bring some of the automation and small batch production home will likely be a growing trend in the near future. Diverse sourcing will be the key to building stronger, smarter supply chains and ensure quick and lasting recovery in case of crisis.
Now is the time to not only set aside a plan B but also a plan C
Takeaway:
Rethink your dependencies on supplies from only one region. Now is the time to not only set aside a plan B but also a plan C. Network with manufacturers from different regions or companies such as AdvaCare that have global production capacity, which is able to shift resources to ensure production capability. Design a smarter and stronger list of your liaisons and have their contact on hand for the times of need. In this way you will be able to depend less on only one supply chain track and, in disruption times, plan ahead and pick the supplier and route from a country less affected by the problem. This will assure the timely delivery of your order to your warehouse even in times of crisis.
Key Challenge #2
Price Increases due to Material Shortages
It is a well-known fact that on a global scale, China and India dominate API production for generic drugs. Recently, with the shutdown and effort of limiting the spread of Covid-19, this has even more clearly shown how heavily pharmaceutical chains rely on these two countries.
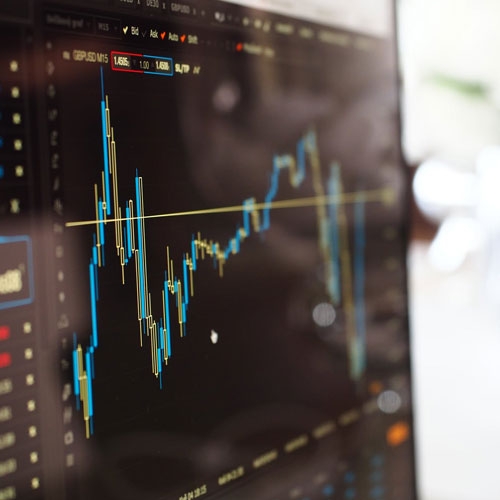
Low availability and increased struggles with transport resulted in many factories worldwide suffering from a sudden shortfall in raw materials. However, material shortages are nothing new and many industries have suffered similar struggles, when their main raw material hubs were affected by higher forces. For example, one global electronics manufacturer lost 16% of revenue in 2016 because of earthquakes in one of the Japanese cities, from where the company was sourcing important parts for its product manufacturing. Moreover, one global automaker lost $5 billion in sales due to floods in Thailand, which resulted in similar issues. Unfortunately, pharmaceutical companies have not learned from past mistakes of other industry leaders. This is why it is important to rethink global models and material supply dependencies. To adapt, more agile and strategic procurement organizations may emerge, as reorganizing assets and supply chains will create more resilience. After, when sourcing from multiple key providers, companies have to learn to move quickly and activate secondary suppliers from non-affected parts of the world even before their inventory is at critical levels. Finally, companies should also focus on production scheduling agility, meaning to clearly plan out what product will be produced in the event of raw material shortages, especially when a component can be used in multiple goods.
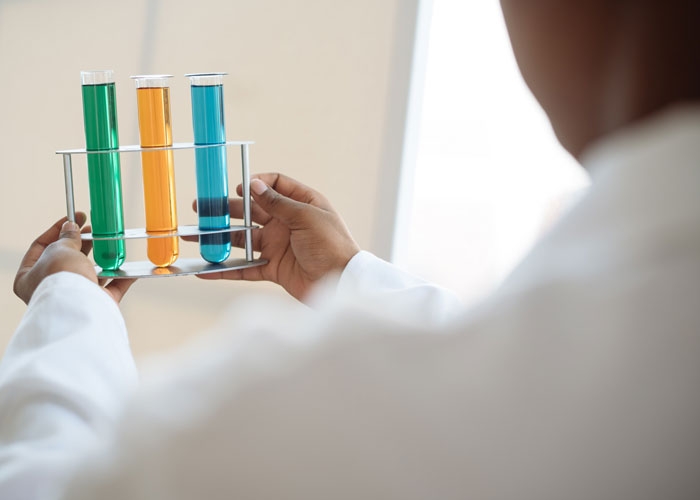
Takeaway:
Even if you are distributing final products and do not have to deal with material sourcing, it is best to diversify your product portfolio as some specific products can become hard to find at one point in time, even if you are working with most trusted suppliers. Imagine that in Covid-19 times you would have only been dealing with PPE products, which were at one point impossible to find, and usually only granted to official government orders. How would your business survive the tough months? Therefore, make sure adaptability and diversification are well known to your business management team and used in everyday strategy planning.
Key Challenge #3
Fear of Demand Drop After Overstocking
It is important to keep in mind that even when the pandemic will pass, and the global economy will get back to its normal functioning, global supply should keep being approached differently. If in the past many companies were aiming to the lowest inventory level possible, this will increase risks in the new reality. Supply chains have truly changed on some fundamental levels.
No business should rely heavily on only one, lowest-cost supplier and minimal product stock to keep business afloat and successful
However, Covid-19 is not the one to blame. Truly it has made professional leaders overthink established processes, but this was long overdue. In the past, many crises have influenced the goods supply network, though none of them were felt worldwide and to such extent as the current pandemic. Remember the SARS outbreak in 2002? Or another example, a climate-related disaster of Katrina hurricane? Recently, even political changes with Brexit and the US-China trade war had influenced supply flows heavily. And as disruptions are increasing in frequency and magnitude, they are becoming almost unavoidable. Therefore, no business should rely heavily on only one, lowest-cost supplier, and minimal product stock to keep business afloat and successful. Even more, doing so is posing a major risk. Evidence shows the severity of individual disruptions is growing and thanks to globalization and automation one can easily spread from local parts to entire systems, which was nicely shown by coronavirus effects in its beginning. When Chinese factories closed, manufacturers struggled to pivot or find other suppliers, and consequences were felt in the global industries even before local lockdowns and outbreaks occurred in other parts of the world.
Takeaway:
Fluctuations in purchasing patterns are the fact of the future. Even if on a smaller scale, they have been happening before the coronavirus outbreak and will happen in the future. As a part of a larger supply chain, distributors can not avoid it. The best solution is to embrace the new reality, be aware of it and work towards knowledge of risk management, visibility into potential supply chain problems, agile and transparent operations, and training of a flexible, collaborative workforce. Only by achieving increased control over every step of the business management, solutions can come and respond to demand changes can be implemented.
Don't want to miss the next AdvaCare article?

Recommended Content
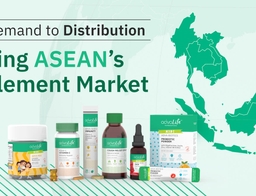
ASEAN Wellness Boom: Strategies for Supplement Distributors to Succeed in a Growing Market
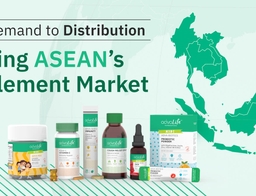
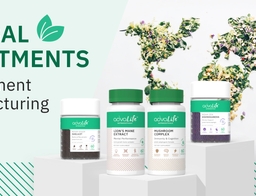
How Growth in Herbal Treatments is Fueling Shifting Supplement Manufacturing Trends
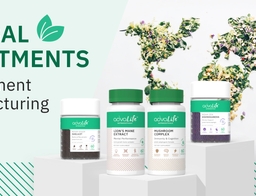
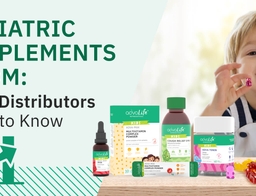
Shifting Trends in Child Wellness: How Savvy Distributors Can Leverage Changing Perceptions
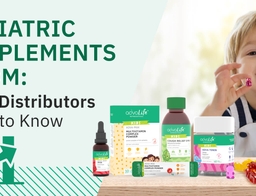